When it comes to the overall design of the waste pyrolysis plant, the reactor is essentially an extremely important part. And it was indeed the major part of several projects that were carried out across different energy industries. However, the initial size of the heating reactor was based mainly on the initial size of the system. Read on as we dive further into the design aspect of the pyrolysis reactor.

The pyrolysis reactor was designed in order to allow the maximum amount of raw materials to be fed into the machine. Due to this, a relatively small amount of time was needed for vapor residence within the reactor. This would then lead to pretty high yield value for the produced pyrolysis oil or rather liquid product.
In order to obtain the max from liquid production, the residence time is the most important factor when it comes to dealing with both volatile gases and liquids alike. Hence the design was kept simple and a cylindrical shaped reactor was brought on stream. Additionally, the reactor was made from stainless steel due to how corrosive pyrolytic fluids actually are. And the reactor stood at a maximum height of 990 mm while it featured a 400 mm diameter. More detailed parameters about tyre recycling machine can be found from the website.
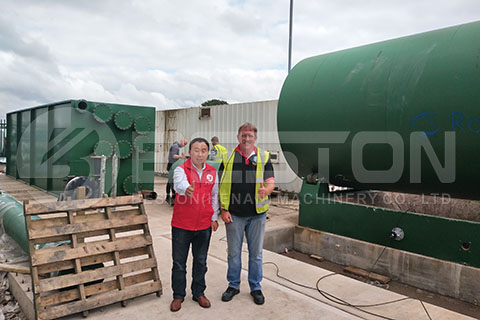
The pyrolysis reactors feeder was that of the through type and it contained a 250 mm diameter and it was covered by a flat plate and some nut-bolts. However, on the inner portion, you’d find semi-hex pipes and three u-shaped spirals that seemed to have a diameter of 19 mm. The final length of the spiral pipes were 1370 mm and the radius was roughly 76 mm. The pipes contained within the reactor were simply used to ensure that faster heating was achieved.
In order to remove the charred bits, there was a 200 mm diameter through at the bottom of the reactor. Additionally, there was also a reactor shield that was constructed of thick 2 mm mild steel and its outer side was made from GP sheet that was also 2 mm. The final length of the furnace was roughly 249 cm and the reactors shield length was 60.96 cm with an internal diameter of 4 cm.
However, the pyrolysis reactors shield is considered as being one of the most important components and is comprised of 4 parts. And two of them are fixed while the others are portable. Additionally, the pyrolysis reactors shield consisted of glass wool that was used for the purpose of insulation. Along with the shield, there was also a burner that was used for either gas or oil.
In order to achieve proper firing, you’ll need a proper burner. And of course, this is used to ensure that the optimum temperature is achieved for operations. Hence two burners were designed and installed on both sides of the furnace. And they even allowed fuel and air to flow directly into the furnace during pyrolysis.
As we conclude we have just looked at the overall design of the tyre pyrolysis plant. And we have even discussed two major components of the reactor. So, keep in mind that your reactor size is fully dependant on your overall system size!